The following article explains how shorter change over time, more flexibility & higher process reliability can be achieved due to several aspects:
1) Seamlessly switch between production setups
2) Reduce switching costs for operators
3) Use data transparency to improve process
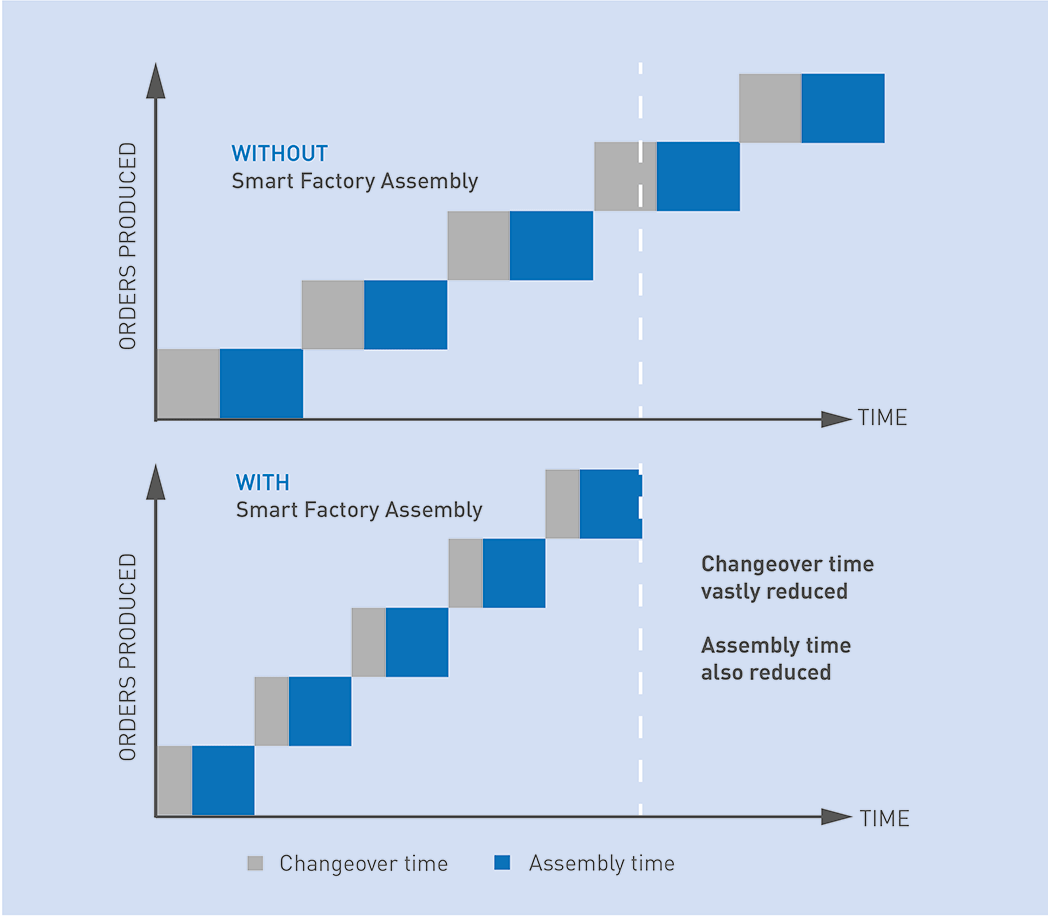
1) Seamlessly switch between production setups
Smart factories and assembly processes require cleverly designed physical setups.
Connected tool integration allows settings, calibration, and configuration information to be saved within the software and automatically updated and transmitted so that each screw and rivet is tightened according to specifications. With tool settings and requirements being automated and monitored, operators don’t have to remember the required torque, parameters, etc. for each step in the process. Pick-by-light applications, rotating assembly towers, and other smart devices can be integrated to reduce the time that operators spend searching for assembly parts – a leading cause of slowdowns in manual assembly processes.
During assembly, input from smart tools or sensors, like scanners or cameras, can be used to advance work instructions and reset tools for the next step in the process. Similarly, triggers can be set to move between different products and variants. Smart device integration and work instruction management make the physical changeover between one production order and the next one as seamless as moving from step to step within an assembly process.
Digitizing your workplace also allows you to change the layout of workstations with just a few mouse clicks, for example from a single workstation to a small production line, giving you the flexibility to change and manage the output of your products.
2) Reduce switching costs for operators during assembly
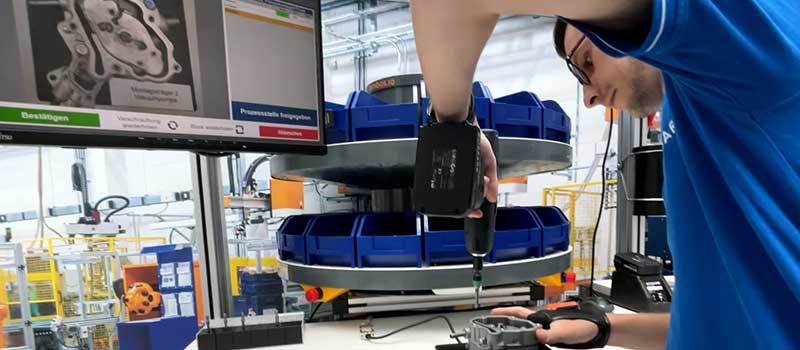
By coupling smart devices and digitized work instructions, complexity during changeovers will be reduced for the employees, and best practices according to Poka-Yoke principles can be applied. This not only increases operator effectiveness by reducing time, but also assures quality standards are adhered to and reduces errors and rework.
In most HMLV environments, operators aren’t exposed to single products or variants long enough or often enough to become experts. Therefore, assembly steps that can’t be physically automated must be communicated via work instructions.
Manual work instructions support the workers to get their job done, but still comprise many uncertainties and time loss in changeovers: is the appropriate document and the right version at hand, which parts are already assembled, what’s the next step. The resulting insecurity and the pressure to do everything right and quickly can negatively influence the well-being of the operator and thus the quality of work.
Digital work instructions reduce cognitive switching costs, allowing operators to maintain their workflow. Workers are guided step by step through the assembly process. Each executed task is confirmed by the operator to proceed to the next task. If desired, operators can add comments to the work instructions during assembly to improve work steps or the workflow. The instructions are accompanied by pictures or graphics, which makes the instructions easy to understand, even for new employees. In this way, also complex assembly tasks are carried out correctly.
3) Use data transparency to improve the process
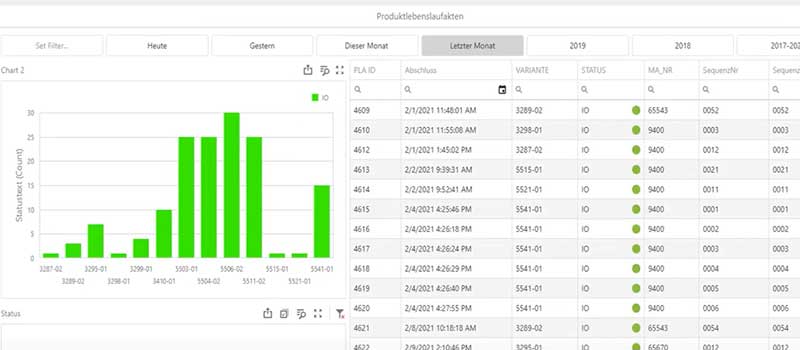
The digitalization of production does not only increase flexibility by making changeovers more efficient from both a physical and human perspective, it also helps strengthen capabilities for the future.
Production data from the digital work instructions and all connected tools and devices, from DC screwdrivers and cobots to measuring systems and testing machinery, are collected at every step, providing unprecedented transparency into operations. This data can be used to monitor and assure quality and can also be used to enable continuous improvement initiatives to design assembly processes to be even more flexible and efficient in the future.