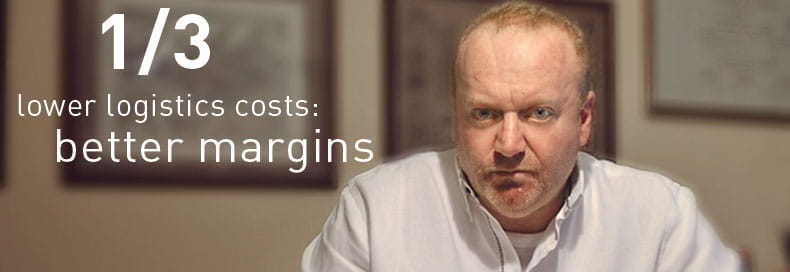
Luca Maria Introini, Logistics Manager, Bossard Italy
"Full-steam ahead with the high-speed train"
After several years in the financial division of different international companies, I got the opportunity to take the lead of the logistics department of Bossard Italy. Right after my start I was involved in a huge project for Alstom.
Honestly, I had to think twice when considering whether to take on this challenge. However, we needed a manager for a project in Piemont, and it didn’t involve finances or Barolo, Brasato or other amenities. Rather we were tasked with installing and commissioning 11 SmartBin systems with a total of 2 500 scales – at night and in one week. The client was the French Alstom Group, a major international client of Bossard. But let me start at the beginning.
Automated purchasing process and C-parts close to production
The project involved the Alstom plant in Savigliano, a small town not far from the French border. Alstom builds its famous Pendolino tilting trains there. In early 2013 Bossard received the order to equip the four production lines at the plant with its SmartBin logistics system. By automating the purchasing process and moving the warehouse for C-parts closer to production, Alstom sought to reduce its logistics costs.
As I mentioned, we had to work at night because Alstom wanted to avoid disruptions to production or delays in deliveries caused by the installation of our SmartBin units. The shift began at 6 p.m. and ended at 6 a.m. That applied to me, as well. I wouldn’t think of leaving my guys in a bind although as the project manager I also had to be available during the day for countless meetings. I didn’t sleep a lot during that time!
The second challenge was that I had to direct a truly multicultural Bossard team. That was the best experience for me. I liked seeing how Bossard employees are cut from the same cloth, so to speak, no matter where they are from. Everybody was on time, goal-oriented, efficient and reliable. Sure, there were differences in the details. The Italians always thought first before taking action. The Swiss were faster, because they had thought things through in advance. And the French team members were in between.
But today, when I see the satisfied faces at our client, then I know that it was good to take on the challenge. We ordered shelves, programmed computers, assembled miles of cables, and worked at full-steam tightening screws, connecting elements and hooking up wiring – and from one day to the next, the SmartBin logistics system was up and running at Alstom. Smoothly. That was a logistics tour de force, and we are confident that our client will enjoy significantly lower logistics costs.
Ref. BIT-CL-TR-01014