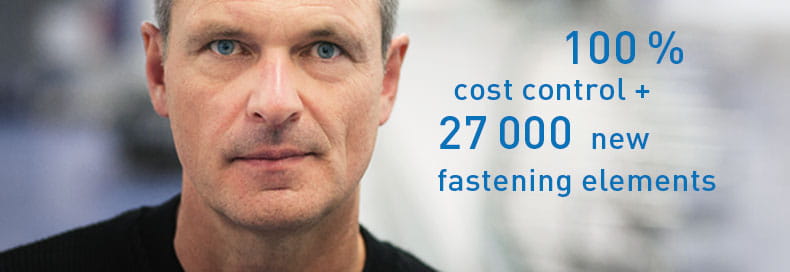
Alain Berenbach, Mechanical Designer, Gebo Cermex, France
"A screw to quench your thirst"
Basically, there is nothing easier than transporting a bottle from point A to point B. All you need is a conveyor in relatively good condition that follows the basic rules for the connections between the two machines. As a specialist for conveyors in the bottling system market, Gebo Cermex designs and installs this type of equipment 365 days a year. It gets complicated when the area near the production line is subject to large temperature fluctuations that require maintenance – which is often difficult to perform. Costs quickly spiral out of control and the client complains that the equipment delivered no longer works after a short period.
Extreme temperatures and penetrating sand stress the components
For our brewery clients, we manage entire production lines. In my role as a mechanical designer, I recently handled a case involving a production line in an open-air factory in equatorial Africa, where the equipment was subjected to extreme wear and tear. There our components are exposed to climate conditions vastly different from those they were created for. Temperatures at the site fluctuate by 15° to 20° Celsius. In addition, the fact that this is an open-air facility created even larger problems for the components because the extreme temperatures were compounded by penetrating sand. The challenge we had to overcome was as extreme as the conditions in which our systems were installed.
Special parts for plastic guide
We found a solution in a relatively short time by incorporating a team of engineers from Bossard in our project. Working at their own locations, the engineers were able to provide a part specially adapted to our new plastic guide. And the costs were low. The problem we faced was the expansion of the plastic. The part that matched our needs most closely was a screw with a square head. It had to be placed between the stainless steel body and the plastic section, but the head was too big. So we had to create an element with a smaller head, which would be as resistant – and as affordable – as possible.
The Bossard teams developed this element for us and brought in specialists who optimized the sequence of individual compression procedures and reduced them to a minimum – because each additional compression step adds to the price of the item. In parallel, our teams tested the tightening torque. We tested the new screw in our laboratory in Reichstett using an impact screwdriver. The part was approved and we started normal production for the new guide via Bossard. We will test the guide in the near future in a new production line in southern France. With a magnitude of 27 000 units a year, it is easy to understand how important such a partnership can be. The impact is enormous. The development of further application opportunities for this new screw will increase demand and further reduce its unit price. We are now working toward achieving this goal.
Ref. BOS-AE-MA-01614